Laminated Veneer Lumber Manufacturing Plant Project Report 2024: Industry trends and Plant Setup
Laminated Veneer Lumber Manufacturing Plant Project Report
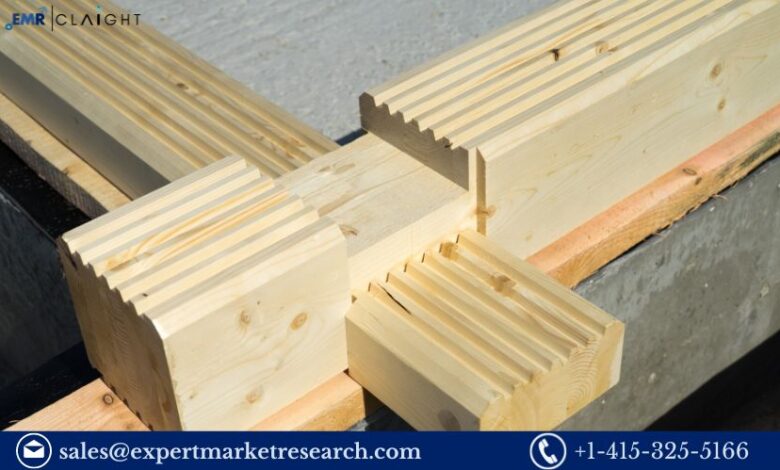
Introduction
Laminated Veneer Lumber (LVL) is an engineered wood product made by bonding together thin layers of wood veneers. It is known for its strength, stability, and versatility, making it a popular choice in construction and furniture manufacturing. As the demand for sustainable and high-performance building materials rises, establishing a Laminated Veneer Lumber manufacturing plant offers a promising business opportunity. This Laminated Veneer Lumber Manufacturing Plant Project Report outlines the key components of setting up such a facility, including project objectives, production processes, market potential, financial projections, and frequently asked questions (FAQs).
Project Overview
Objective
The main objective of this project is to create a state-of-the-art manufacturing plant for producing high-quality LVL products. The facility will focus on sustainable practices, innovative technologies, and meeting diverse customer needs.
Location
Choosing the right location is crucial for the success of the manufacturing plant. Important factors to consider include:
- Proximity to Raw Material Suppliers: The facility should be near sources of high-quality wood veneers to ensure a steady supply.
- Transportation Infrastructure: Access to major roads and shipping routes will facilitate the distribution of finished products.
- Labor Availability: The chosen location should have access to a skilled workforce familiar with wood processing and manufacturing.
Capacity
The proposed plant will have an initial production capacity of 20,000 cubic meters per year, with the flexibility to scale up based on market demand.
Get a Free Sample Report with Table of Contents @
Production Process
Raw Materials
Key raw materials required for LVL manufacturing include:
- Wood Veneers: Thin layers of wood that are glued together to form LVL.
- Adhesives: High-quality adhesives are essential for bonding the veneers and ensuring durability.
Manufacturing Steps
- Veneer Production: Logs are debarked and sliced into thin sheets, or veneers, using specialized machinery.
- Drying: The veneers are dried to a specific moisture content to enhance bonding strength and prevent warping.
- Adhesive Application: A suitable adhesive is applied to the dried veneers, preparing them for layering.
- Layering: The adhesive-coated veneers are stacked in layers, typically with the grain direction of adjacent layers perpendicular to each other for added strength.
- Pressing: The layered veneers are placed in a hydraulic press, where heat and pressure are applied to cure the adhesive and bond the layers together.
- Trimming and Finishing: The cured LVL is trimmed to desired dimensions, sanded, and inspected for quality.
- Quality Control: Rigorous testing is performed to ensure that the final product meets industry standards for strength, durability, and appearance.
- Packaging: The finished LVL products are packaged and prepared for distribution to customers.
Market Potential
Demand Analysis
The demand for LVL is driven by several factors:
- Construction Industry Growth: As urbanization and infrastructure development increase, the demand for strong and reliable building materials rises.
- Sustainability Trends: LVL is made from renewable resources, making it an attractive choice for environmentally conscious builders and architects.
- Versatility: LVL can be used in various applications, including beams, columns, and roof trusses, making it suitable for a wide range of projects.
Competition
While the market includes established players, there is still room for new entrants focusing on innovation and sustainability. Creating a strong brand identity and effective marketing strategies will be crucial for capturing market share.
Financial Projections
Initial Investment
The estimated initial investment for the LVL manufacturing plant includes:
- Land and Infrastructure: $800,000
- Machinery and Equipment: $1.5 million
- Raw Materials: $200,000
- Working Capital: $300,000
- Miscellaneous Costs: $50,000
Total estimated investment: $2.85 million.
Revenue Generation
With an anticipated selling price of $600 per cubic meter and an initial production capacity of 20,000 cubic meters per year, projected annual revenue could reach $12 million. After accounting for operational costs, a profit margin of approximately 15-20% is expected.
Break-even Analysis
The break-even point is projected to be achieved within the first 3-4 years, depending on effective marketing strategies and market conditions.
Environmental Considerations
Sustainability is a key focus in modern manufacturing. The LVL manufacturing plant will implement eco-friendly practices, including:
- Sustainable Sourcing: Prioritizing wood from certified sustainable forests to minimize environmental impact.
- Waste Management: Developing a waste reduction program to manage by-products and minimize emissions.
- Energy Efficiency: Investing in energy-efficient machinery and processes to reduce the plant’s carbon footprint..
FAQs
1. What applications does Laminated Veneer Lumber have?
LVL is used in various applications, including beams, headers, trusses, and furniture, providing structural support and design flexibility.
2. How long does it take to set up an LVL manufacturing plant?
Setting up the plant typically takes around 12-18 months, including site selection, construction, equipment installation, and obtaining necessary permits.
3. What safety measures are implemented in the production process?
Safety measures include regular maintenance of equipment, adherence to safety regulations, and comprehensive training for employees on machinery operation and safety protocols.
4. What is the expected return on investment (ROI)?
With a projected profit margin of approximately 15-20%, the ROI is expected to be realized within 3-4 years of full-scale operations.
5. Are there grants or subsidies available for setting up this type of plant?
Yes, various grants, subsidies, or tax incentives may be available for businesses focused on sustainable wood products. Researching local government programs is advisable.
6. What are the key factors for success in the LVL manufacturing industry?
Key factors include maintaining high product quality, effective marketing strategies, compliance with safety regulations, and innovation in product design.
Related Reports
https://www.expertmarketresearch.com/reports/incident-and-emergency-management-market
https://www.expertmarketresearch.com/articles/top-digital-marketing-companies
https://www.expertmarketresearch.com/reports/plastic-additives-market
Media Contact:
Company Name: Claight Corporation
Contact Person: Lewis Fernandas, Corporate Sales Specialist — U.S.A.
Email: sales@expertmarketresearch.com
Toll Free Number: +1–415–325–5166 | +44–702–402–5790
Address: 30 North Gould Street, Sheridan, WY 82801, USA
Website: www.expertmarketresearch.com
Aus Site: https://www.expertmarketresearch.com.au