Top Maintenance Tips for Extending the Life of Used Metalworking Machinery
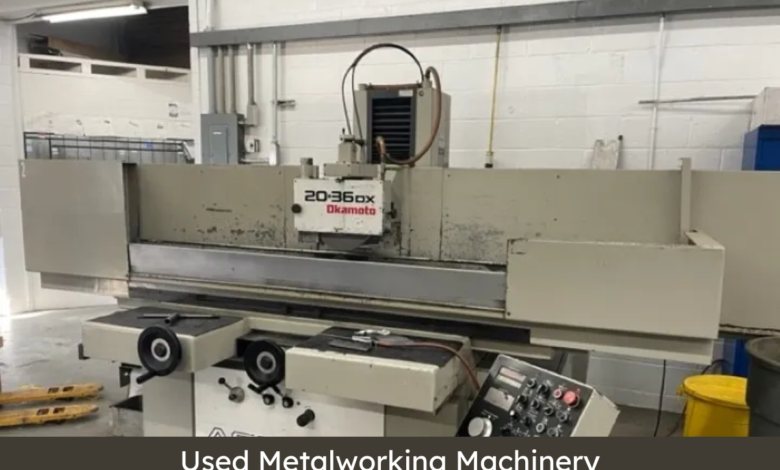
Purchasing Used Metalworking Equipment can be a cost-effective solution for businesses seeking high-quality tools at a lower investment. However, to get the most out of your equipment, regular maintenance is crucial. Used machinery often shows signs of wear, making upkeep even more essential. Proper maintenance not only extends the life of your machinery but also ensures consistent performance, reducing downtime and unexpected repair costs. In this blog, we’ll explore some top maintenance tips to help you maximize the longevity and efficiency of your used metalworking machinery.
1. Establish a Preventive Maintenance Schedule
One of the most effective ways to extend the life of your used metalworking machinery is to implement a preventive maintenance schedule. Waiting until something breaks down can be costly, both in terms of repair and production delays. Regular inspections and maintenance can help you catch small issues before they become major problems.
Create a checklist that covers all critical components of your equipment. This checklist should include:
- Lubrication of moving parts
- Inspection of wear and tear on belts, gears, and bearings
- Checking for loose bolts or connections
- Testing electrical and hydraulic systems
Adhering to a strict schedule can prevent unexpected failures and increase the reliability of your machinery.
2. Keep Machinery Clean and Free from Debris
Metalworking machinery is exposed to a variety of materials, such as metal shavings, dust, and oils, which can accumulate and affect performance. One of the easiest but often overlooked maintenance tasks is keeping the equipment clean.
Debris buildup can cause blockages, leading to reduced machine efficiency or even damage. Here are some cleaning tips:
- Regularly wipe down surfaces, especially around critical parts.
- Use compressed air to clean hard-to-reach areas.
- Pay special attention to ventilation and cooling systems to prevent overheating.
Taking the time to clean your used metalworking equipment helps maintain smooth operation and can prevent long-term damage caused by contamination.
3. Lubricate Moving Parts Regularly
Lubrication is one of the most important aspects of machine maintenance. The moving parts of your used metalworking equipment, such as bearings, gears, and slides, are subject to friction and wear over time. Without proper lubrication, these parts can seize or wear out prematurely, leading to costly repairs or replacement.
Make sure to:
- Use the correct type of lubricant recommended by the equipment manufacturer.
- Follow a lubrication schedule, ensuring you don’t miss any vital components.
- Check lubricant levels frequently and top up as needed.
By keeping all moving parts well-lubricated, you can reduce friction, wear, and tear, ultimately prolonging the life of your machinery.
4. Conduct Regular Alignment Checks
Proper alignment is critical for the efficient operation of metalworking machinery. Over time, components can become misaligned due to vibration, improper use, or general wear and tear. Misaligned machinery can lead to inaccurate cuts, increased wear on parts, and even machine failure.
To avoid these issues:
- Periodically check the alignment of key components like shafts, spindles, and worktables.
- Use specialized tools to ensure precision alignment.
- Address any issues immediately to prevent further damage to your machinery.
Regular alignment checks help maintain the accuracy and efficiency of your equipment, ensuring consistent performance and reducing the risk of costly downtime.
5. Replace Worn Parts Proactively
Every machine has parts that will wear out over time, especially when dealing with used metalworking equipment. Instead of waiting for a component to fail, be proactive about replacing worn parts. This is especially important for consumable parts like belts, bearings, and cutting tools, which can directly affect machine performance.
Some proactive measures include:
- Keeping spare parts on hand to reduce downtime when replacements are necessary.
- Inspecting parts regularly for signs of wear, such as cracks, thinning, or rust.
- Using only high-quality replacement parts that meet the original manufacturer’s specifications.
By replacing worn components before they fail, you can avoid costly repairs and keep your machinery running smoothly.
6. Monitor Electrical and Hydraulic Systems
The electrical and hydraulic systems of your used metalworking machinery are crucial for its operation. Faulty electrical components can lead to machine malfunctions, while issues with the hydraulic system can cause pressure loss, overheating, and poor performance.
To ensure these systems are functioning properly:
- Inspect electrical wiring for signs of wear, such as fraying or exposed wires.
- Test electrical connections regularly and replace any faulty components immediately.
- Check hydraulic fluid levels and monitor for any leaks or pressure issues.
- Replace hydraulic filters as needed to maintain clean fluid flow.
Proper care of these systems helps maintain the overall functionality of your machinery and prevents unexpected breakdowns.
7. Train Operators on Proper Use
The way your operators use the equipment can significantly impact its lifespan. Training your employees on the correct operation of used metalworking equipment ensures that the machinery is handled with care and used according to its intended purpose.
Here are some training tips:
- Make sure operators understand the machine’s capabilities and limitations.
- Teach operators how to identify signs of wear or malfunction so they can report issues early.
- Provide regular refresher training to keep everyone up to date on best practices.
Proper usage helps prevent unnecessary strain on the equipment, reducing the likelihood of damage and prolonging its lifespan.
8. Document Maintenance and Repairs
Keeping detailed records of all maintenance activities is essential for tracking the condition of your used metalworking machinery. Documenting repairs, replacements, and inspections helps you stay organized and ensures that maintenance tasks are completed on time.
A well-maintained log should include:
- Dates of all maintenance activities
- Parts that were inspected, repaired, or replaced
- Notes on machine performance and any issues encountered
This documentation can be invaluable when troubleshooting issues or when selling the equipment in the future, as it provides proof of diligent care and maintenance.
Conclusion
Purchasing Used Metalworking Equipment can be a wise investment for businesses looking to reduce costs without sacrificing quality. However, without proper maintenance, this equipment can quickly deteriorate, leading to increased expenses and reduced productivity. By following these top maintenance tips—such as establishing a preventive maintenance schedule, keeping the machinery clean, lubricating moving parts, and training operators—you can extend the life of your used metalworking machinery and ensure it continues to deliver reliable performance for years to come.