How Do Roller Chains Compare to Modular Chains for Industrial Use?
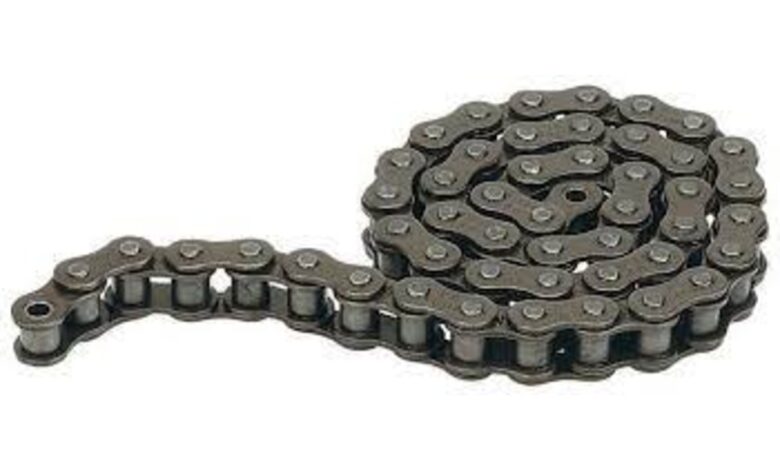
In industrial settings, the choice of chain type can significantly impact machinery performance, maintenance costs, and overall efficiency. Two popular types of chains used in various industrial applications are roller chains and modular chains. Each type has its unique features, benefits, and limitations. Understanding how these chains compare can help you make an informed decision based on your specific needs and requirements. This blog explores the differences between roller chains and modular chains, focusing on their applications, advantages, and considerations for industrial use.
What Are Roller Chains?
Roller chains are a type of chain used extensively in industrial machinery, particularly for power transmission applications. They consist of a series of interconnected links, with rollers that engage with sprockets to transfer motion and force. Roller chains are commonly used in applications such as conveyor systems, motorcycles, and agricultural equipment.
Key Features of Roller Chains:
- Construction: Roller chains are made up of inner and outer links, with rollers that reduce friction between the chain and sprockets.
- Material: Typically made from steel or stainless steel, roller chains are designed for durability and strength.
- Size Variations: Available in various sizes and configurations to suit different power transmission needs.
What Are Modular Chains?
Modular chains, on the other hand, are composed of interconnected plastic or metal modules that form a continuous chain. These modules are designed to snap together, creating a flexible and customizable chain system. Modular chains are often used in conveyor systems and material handling applications where flexibility and easy maintenance are essential.
Key Features of Modular Chains:
- Construction: Modular chains consist of individual modules that can be assembled and disassembled easily, allowing for customization.
- Material: Made from plastic or metal, modular chains offer a range of properties, including resistance to chemicals and high temperatures.
- Design Flexibility: The modular design allows for easy modification and expansion of the chain system.
Comparing Roller Chains and Modular Chains
To understand how roller chains and modular chains compare, let’s examine their performance, advantages, and limitations in various industrial applications.
- Durability and Strength
- Roller Chains: Known for their robustness and ability to handle high loads, roller chains are ideal for heavy-duty applications. They are designed to withstand significant stress and can operate in harsh environments. However, they require regular lubrication and maintenance to ensure optimal performance and longevity.
- Modular Chains: While modular chains are generally less robust than roller chains, they still offer good durability for many applications. They are designed to handle moderate loads and are less prone to stretching or elongation. Modular chains often require less maintenance compared to roller chains, but their load-bearing capacity may be limited compared to heavy-duty roller chains.
- Maintenance and Lubrication
- Roller Chains: Regular maintenance is crucial for roller chains to ensure smooth operation. This includes lubrication to reduce friction and prevent wear. Proper maintenance extends the lifespan of the chain and prevents potential breakdowns. However, this maintenance can be time-consuming and may require downtime for the machinery.
- Modular Chains: Modular chains typically require less maintenance than roller chains. They do not need lubrication, as they do not rely on rollers or metal-to-metal contact. The modular design allows for easy replacement of individual modules, reducing downtime and simplifying maintenance procedures.
- Flexibility and Customization
- Roller Chains: Roller chains are generally fixed in their design and require specific sprockets for operation. While they are versatile in terms of power transmission, they offer less flexibility for modifications or adjustments once installed.
- Modular Chains: Modular chains excel in flexibility and customization. The modular design allows for easy adjustments and modifications, making them suitable for applications that require frequent changes or expansions. This flexibility is particularly beneficial in conveyor systems where the layout or configuration may need to be altered.
- Noise and Vibration
- Roller Chains: Roller chains can generate noise and vibrations during operation due to the metal rollers and sprockets. This can be a concern in environments where noise levels need to be minimized or where vibrations can affect the machinery’s performance.
- Modular Chains: Modular chains generally produce less noise and vibrations compared to roller chains. The smooth operation of the modular design and the absence of metal-to-metal contact contribute to quieter and more stable performance.
- Cost Considerations
- Roller Chains: Roller chains are often more cost-effective upfront, especially for heavy-duty applications. However, the need for regular maintenance and lubrication can add to the overall cost over time. The total cost of ownership should be considered, including maintenance and potential downtime.
- Modular Chains: Modular chains can have a higher initial cost due to their design and materials. However, their lower maintenance requirements and ease of replacement can lead to cost savings in the long run. The ability to customize and expand the system can also provide cost benefits for applications requiring flexibility.
Applications of Roller Chains and Modular Chains
- Roller Chains: Ideal for high-torque applications and heavy-duty power transmission. Commonly used in industries such as automotive, agriculture, and manufacturing. Suitable for conveyor systems where heavy loads and high speeds are involved.
- Modular Chains: Best suited for applications requiring flexibility, easy maintenance, and customization. Commonly used in material handling, packaging, and food processing industries. Ideal for conveyor systems with complex layouts or frequent configuration changes.
Conclusion
Choosing between roller chains and modular chains depends on your specific industrial needs and priorities. Roller chains offer durability, strength, and cost-effectiveness for heavy-duty applications but require regular maintenance. Modular chains provide flexibility, low maintenance, and quieter operation, making them ideal for applications that require customization and ease of use.
By understanding the strengths and limitations of each type of chain, you can make an informed decision that aligns with your operational requirements and budget. Whether you prioritize durability, flexibility, or maintenance efficiency, selecting the right chain type can significantly impact your machinery’s performance and overall efficiency in an industrial setting.